Visita a la fábrica de Paul Reed Smith: cómo se construyen las PRS
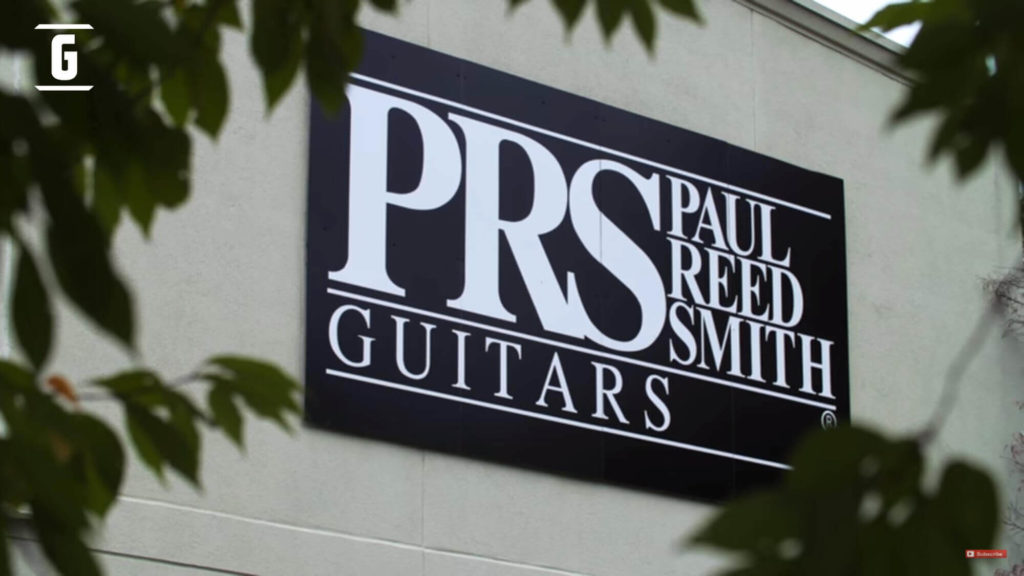
Hace un mes PRS Guitars publicó un video en su página oficial de Youtube con un tour o visita por la fábrica de PRS de Maryland, Estados Unidos, donde muestran y detallan todo el proceso de construcción de las Series Core, S2 y Bolt-on -atornillada- de Paul Reed Smith Guitars.
A continuación te mostramos el video de tour en la fábrica de PRS y transcribimos todo el contenido traducido al español – castellano para que puedas disfrutar y descubrir todos los fascinantes secretos de estas extraordinarias guitarras.
Introducción del Director de Operaciones de la fábrica de PRS USA
¡Hola! Soy Jack Higginbotham -Director de Operaciones de Paul Reed Smith-. Estamos en la fábrica PRS en Stevensville, Maryland, en la costa este. Hoy vamos a hacer un recorrido por la fábrica de PRS. Nos centraremos en las series Core, S2 y Bolt-on.
Más de tres décadas de historia de PRS
Con PRS ya llevamos más de tres décadas, lo cual es un poco extraño de pensar porque no parece que hayamos estado tres décadas ya. Muchas de las personas dentro de esta empresa son las mismas personas que cruzaron las puertas en la década de 1980. De forma que esa continuidad nos permite empujarnos y cambiar, nos permite ser flexibles. Lo que no está cambiando son nuestros principios básicos de lo que significa hacer una buena guitarra y el descubrimiento que viene con eso, es lo que realmente nos impulsa todos los días. Esa es la pasión de hacer la guitarra, esa es la pasión de perseguir el sonido.
Haciendo equilibrio en la construcción de guitarras PRS
Todos los días, cuando entramos en esta fábrica, básicamente estamos entrando en una cuerda floja y estamos realizando un acto de equilibrio y de muchas maneras diferentes. Algunas de esas formas son el equilibrio y el balance entre la historia versus la tecnología y donde estamos impulsando el arte de hacer guitarras. Luego está el equilibrio del arte de la guitarra en sí mismo versus la fabricación y luego eso nos lleva al equilibrio entre la fabricación y las máquinas versus la artesanía en el trabajo manual que se necesita para hacer un instrumento fino.
Asíque salgamos a la fábrica y veamos algunas de las prácticas de las que hemos hablado. Mire algunos de esos actos de equilibrio que hemos discutido y vea lo que vemos.
¡Espero que disfrutes el recorrido!
Recorrido por la fábrica de Paul Reed Smith de Maryland, Estados Unidos
Primera parada: Rough Cut o Primer Corte
La primera parada de nuestro recorrido es en nuestro Rough Cut -primer corte-.
La fabricación de guitarras se compone de materiales diseñados y procesos y en «corte general» es donde recopilamos todos nuestros materiales. Estos materiales forman la base de la guitarra, crea el sonido de la guitarra desde el punto de vista del trabajo en madera.
Una vez que tenemos estos materiales en nuestras instalacioens, depende de nosotros procesarlos, nutrirlos y sacar todo lo mejor que podamos de esta madera para hacer la mejor guitarra posible, y esto comienza con el proceso de secado.
Proceso de Secado de Madera
Debe tener mucho cuidado con el secado del arce -maple- porque el arce rizado –curly maple– es muy sensible y realmente puede dañarse fácilmente si no seca la madera correctamente. Entonces, comenzamos con un proceso de secado con aire donde la madera se empareja como libro -book matching–. El Book Matching es el proceso en el que tomamos un bloque de madera -curly maple- y lo cortamos o aserramos por la mitad en nuestro sierra o molino horizontal y se pliega como las páginas de un libro.
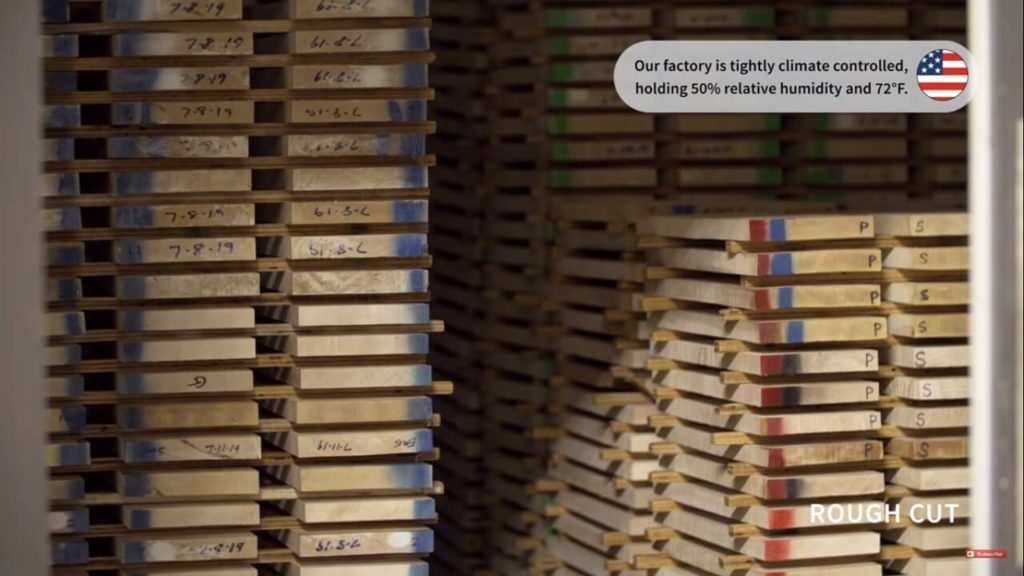
Luego, la madera se coloca en un pallet y se separa con pequeñas piezas de madera para que el aire pueda fluir entre los distintos listones o tablones, y secar lentamente la humedad que hay en ella.
Una vez que reducimos el contenido de humedad a un nivel razonable, podemos colocar la madera en nuestros salones de secado, donde hemos inyectamos el aire caliente que circula en la habitación y nuevamente elimina lentamente la humedad de la madera y la baja a los niveles de humedad en nuestra fábrica.
La importancia del secado de la madera
Lo bien que seque esa madera está directamente relacionado con lo bien que vibrará esa guitarra. También tiene una correlación directa con la forma en que se mantendrá afinada porque si liberas la humedad, la bloqueas, la guitarra se vuelve muy estable. Todavía debe asegurarse de tener un puente de calidad, unas clavijas de calidad y un seteo y ajuste de calidad, que la cejuela esté cortada correctamente y sea de los materiales correctos, todas esas cosas aún pueden arruinar una guitarra fácilmente pero no servirán de nada si no tienes una plataforma estable, es decir un buen mueble.
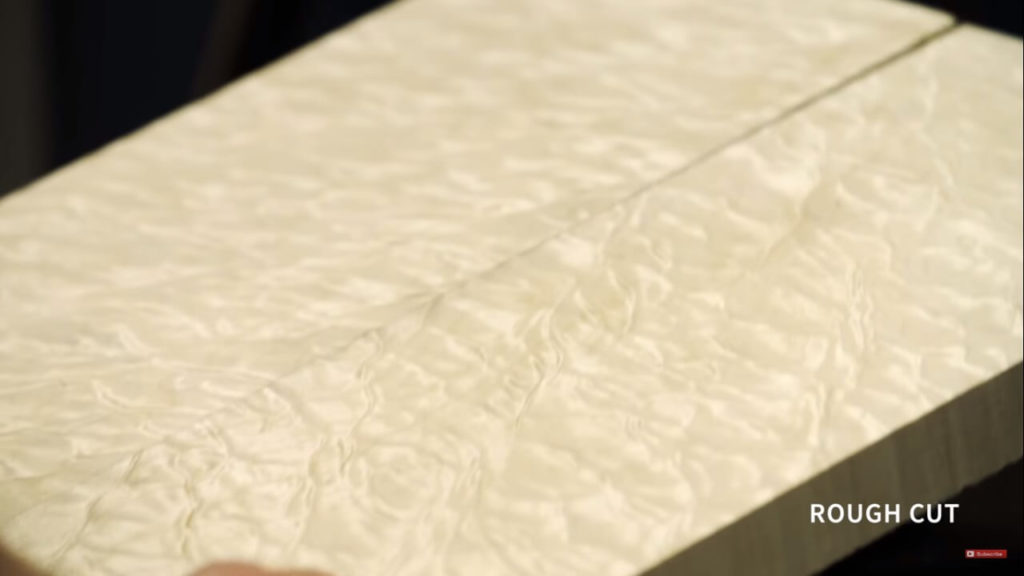
Agrupación de maderas por Serie y por Calidad
Dividimos nuestros materiales básicamente en dos grupos. Tenemos nuestros materiales Core y tenemos nuestros materiales S2 / Bolt-on. Dentro de ambos grupos, usamos un proceso de clasificación, por lo que cuando miras a través de la fábrica y ves pilas de arce rizado -curly maple- con diferentes colores en el extremo, lo que vez es una identificación o etiqueta para diferenciarlos. Es básicamente así, para que podamos construir rápidamente un programa o cronograma de producción y ensamblar nuestras guitarras cada día en función de la demanda de los clientes.
Inlay y diapasón -Inlay & Fretboards-
Antes de comenzar a construir una guitarra, hay una sección de soporte que es la incrustación -inlays- y el diapasones, tastieras o trasteras. Esta es un área que realmente abastece prácticamente todos los aspectos del negocio.
Lijado de espesor
Comienza con el lijado de espesor de los materiales. Primero sacamos la madera de nuestro horno, la aclimatamos en nuestro taller de carpintería y luego la pasamos por nuestra lijadora de espesor y la llevamos al espesor adecuado de un diapasón final.
Corte de contorno, inlays y agujeros de clavijas
Una vez que el diapasón está lijado en el grosor adecuado, lo llevamos a una máquina CNC donde cortaremos el contorno de la guitarra y luego ruteamos los agujeros para las incrustaciones de pájaros o lo que sea el Inlay que va en ese diapasón.
La tapa, enchapado o cubre clavijero también se lija al espesor correspondiente y luego se dirige a nuestra máquina CNC donde cortaremos el perímetro, cortaremos el negativo para la firma y el clavijero y luego cortaremos los agujeros para las clavijas.
Colocación de Inlays y Firma de Paul Reed Smith
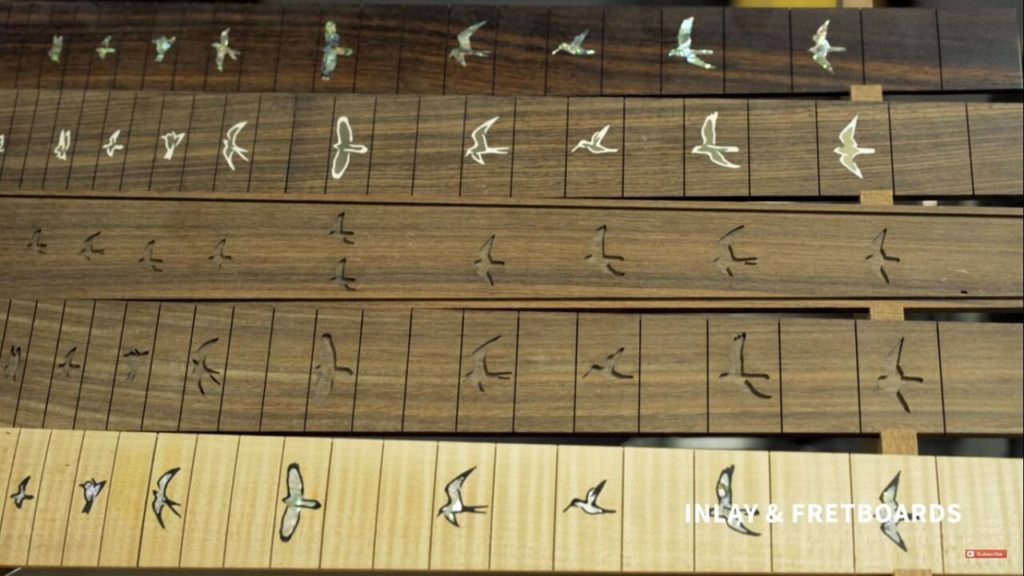
Una vez que el diapasón y el cubre pala están ruteados, se les coloca o incrusta los Inlays y Firma de Paul. En inlay tenemos muchas opciones. Tenemos casos de material de inlay que abarcan muchos años, por lo que tenemos la capacidad de mezclar y combinar y crear muchos diseños e ideas nuevos basados en lo que hemos hecho en el pasado.
Una vez que hemos seleccionado ese material de incrustación o inlay, tomamos el diapasón y pegamos cuidadosamente cada «Bird» –Ave– en su lugar. Pegamos la firma en la chapa del peghead -clavijero-. Luego, se deja curar el pegamento y ya tenemos un juego de diapasón y tapa de clavijero terminado, que están listos para la fabricación.
Contrucción del mango o mástil
Así que ahora tenemos nuestra madera seleccionada y tenemos un diapasón y necesitamos un mástil. Hacer un mango siempre ha sido un proceso muy fascinante para mí, porque es algo complicado y si lo haces bien, realmente está bien y si no lo haces bien, puede salir mal de varias formas diferentes. Es un subcomponente de precisión para hacer una guitarra. Este proceso de mástil es algo que hice en los años 80’s y realmente me encantó.
Objetivos de un buen mástil o mango de guitarra
Un buen mango de guitarra tiene que ser estable, tiene que ser tonal, tiene que ser generalmente muy denso y muy resonante.
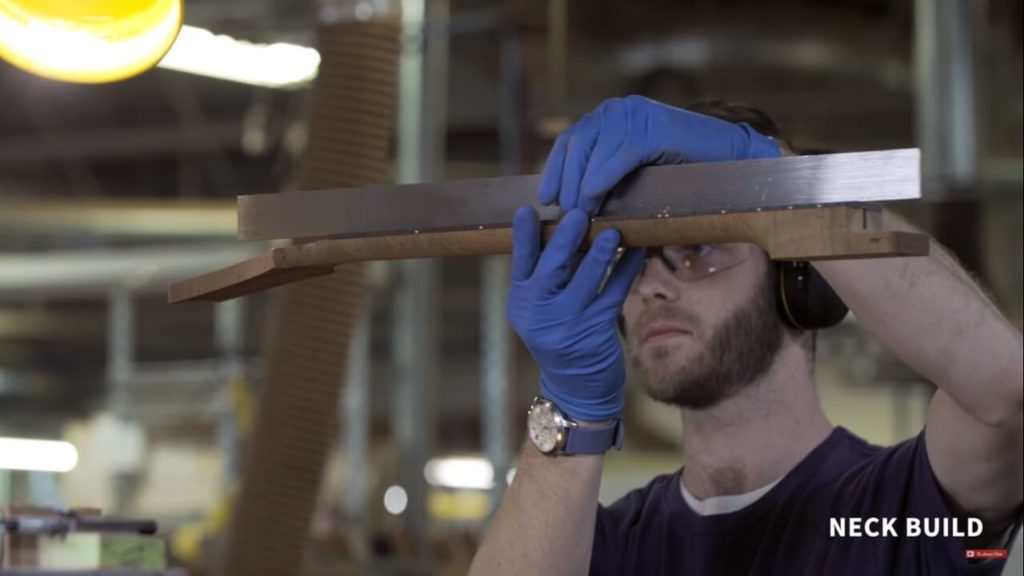
Diferencias entre mástiles S2, Bolt-on y Core
S2, Bolt-on y Core tienen procesos ligeramente diferentes, pero realmente comparten el mismo objetivo. El objetivo es tener ese buen mango.
La Serie S2 se creó en un momento en que necesitábamos aprender a hacer productos de nivel de precio diferente al que estabamos acostumbrados. Estábamos buscando incorporar un nuevo guitarrista a la familia PRS (al guitarrista que compra guitarras de la franja de precios que va de los USD 1.000 a los USD 2.000). Todos estuvimos de acuerdo en que muchas cosas podrían cambiar, pero lo que no comprometeríamos sería la integridad del instrumento basado en el mango, que es realmente el corazón de todo.
Tablones más finos para ahorrar tiempos y costos
Se tarda aproximadamente un mes en hacer un mástil Core de principio a fin. Un mango S2 y un Bolt-on toman una fracción del tiempo porque -el tamaño de la tabla de madera usada- está más cerca del tamaño final de un mástil terminado. -El tamaño del tablón- es de cuatro cuartos -aprox 2,54 cm- en lugar de doce cuartos -aproximádamente 7,62 cm. que se usa para la Core-. Esta diferencia ahorra mucho tiempo del proceso.
La forma en que podemos usar una pieza de madera en bruto de cuatro cuartos para el mango en lugar de una de doce cuartos es con un corte muy preciso para empalmar el mango con el clavijero con el ángulo preciso. Por lo que hacemos un corte muy preciso en una caja de corte de alta precisión. Termina eso con una proceso de CNC que termina con dos piezas de acoplamiento perfecto que, cuando se gira una y se unen, forman nuestro ángulo de pala perfecto.
Luego se corta el extremo del tablón del mango y finalmente se pega a la parte inferior del cuello y eso forma el talón y el lugar donde descansará la recolección del cuello.
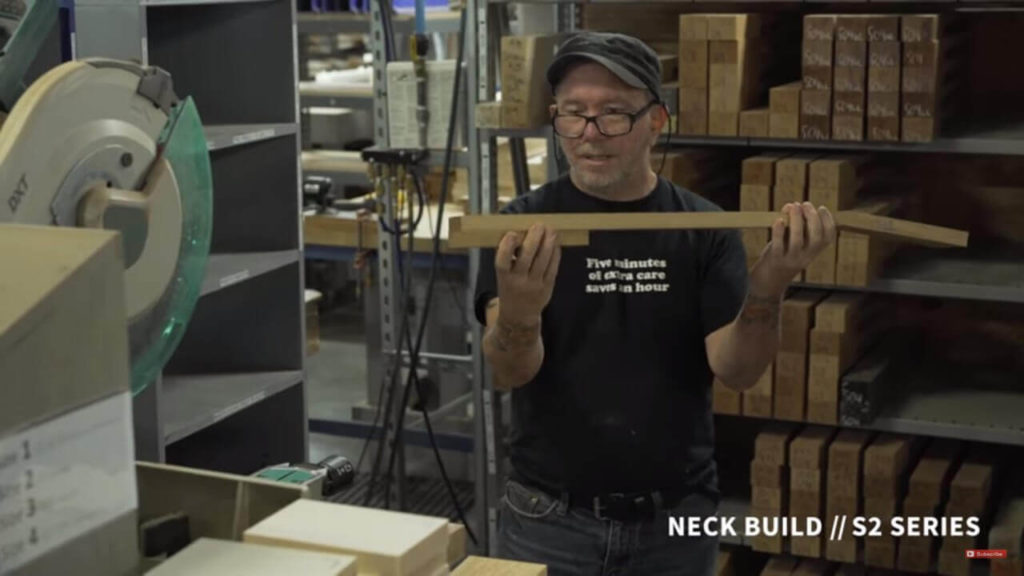
Colocación del tensor y encolado de cubre tensor y diapasón
Una vez que la pala se cortó y se empalmó con el ángulo y se pegó el talón -del neckjoint-. El resto del proceso es muy similar entre las series Core, Bolt-on y S2. Ranuramos el mango para el alma, instalamos un tensor de doble acción, luego pegamos un un cubre tensor de madera en la ranura, presionamos el cubre tensor dentro del mango en los mismos espacios que finalmente sujetaremos el diapasón al cuello, cuando se seca el pegamento, se limpia, cortará la superficie, se pega el diapasón usando un sistema de agujeros para que encastre perfecto y se continua con á el proceso de fabricación del mástil.
Proceso de tallado del mango y radiado del diapasón
Después de que el diapasón y el mástil se hayan pegado, pasamos a nuestro programa de tallado. Una vez que el mango está tallado, listo para redondear el nivel y el traste. El redondeo del diapasón se realiza primero en una máquina CNC a partir de ahora viene mucho trabajo manual.
La primera parada del trabajo manual es el radio y la nivelación del diapasón. Para esto se usa una plantilla de aluminio con un operador u artesano altamente calificado que asegurará que tengamos un radio perfecto, que sea muy consistente desde la cejuela hasta el talón y también tengamos un diapasón perfectamente nivelado desde la cejuela hasta el talón.
Colocación de trastes o entrastado
Una vez que tengamos esa plataforma perfecta, seguiremos con la colocación de trastes. El entrasteado hecho a la perfección nos permitirá poner una gota de pegamento en cada ranura del traste, presionar cada traste de forma consistente y pareja para que terminemos con un radio de diapasón muy plano muy bien. Luego tenemos trastes que se presionan de manera muy pareja y para cuando nivelamos los trastes en nuestro proceso de finalización. Al final queda muy poco material que necesitemos eliminar para asegurarnos de que esa superficie de ejecución sea absolutamente perfecta.
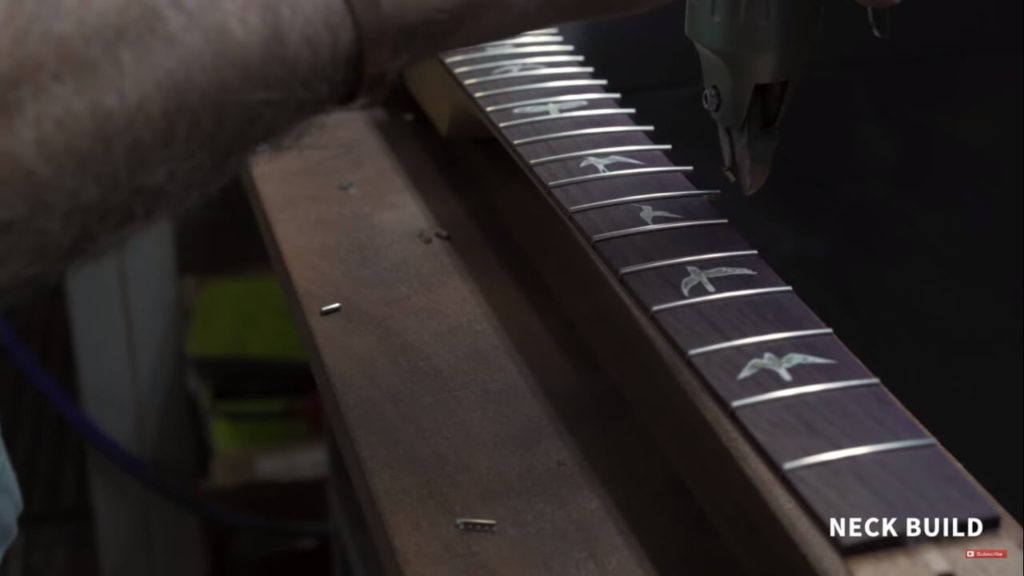
Utilización de máquinas vs proceso a mano
Desde el comienzo de la empresa, hemos sido muy cuidadosos al pensar en cuáles son las tareas en las que se debe utilizar una máquina y cuáles son las operaciones en las cuales un artesano experto debe ser el responsable.
En general, una máquina se puede utilizar para procesos muy repetitivos, pero un artesano es absolutamente esencial para asegurarse que cuando un guitarrista coloque las manos sobre el mango, este se sienta perfecto. Una persona entiende lo que el guitarrista quiere sentir, sentir la comodidad y hacer que el mango quede de esa forma. Hacemos mucho trabajo a mano en las tareas de lijado.
Construcción del cuerpo de la guitarra
Pegado de tapa de maple
En comparación al mango, un cuerpo es algo bastante simple de hacer. Comenzamos con un fondo y una tapa de arce aparejada utilizando el «booking matching» y los pegamos en nuestra prensa de pegado. La prensa tiene una presión de entre 6.500 -aproximadamente 3.000 kilos- libras y aproximadamente 7.500 libras -aproximadamente 3.400 kilos-. Esto equivale al peso de una camioneta grande -una Chevrolet Suburban- encima de cada una de estas pilas de cuerpos.
Algunas guitarras son de cuerpo sólido sin tapa de arce, y pasan por alto ese proceso de pegado de tapa. Simplemente son dos tablones de madera pegados, unidos y cepillados, luego están listos para el proceso de corte, listos para el CNC.
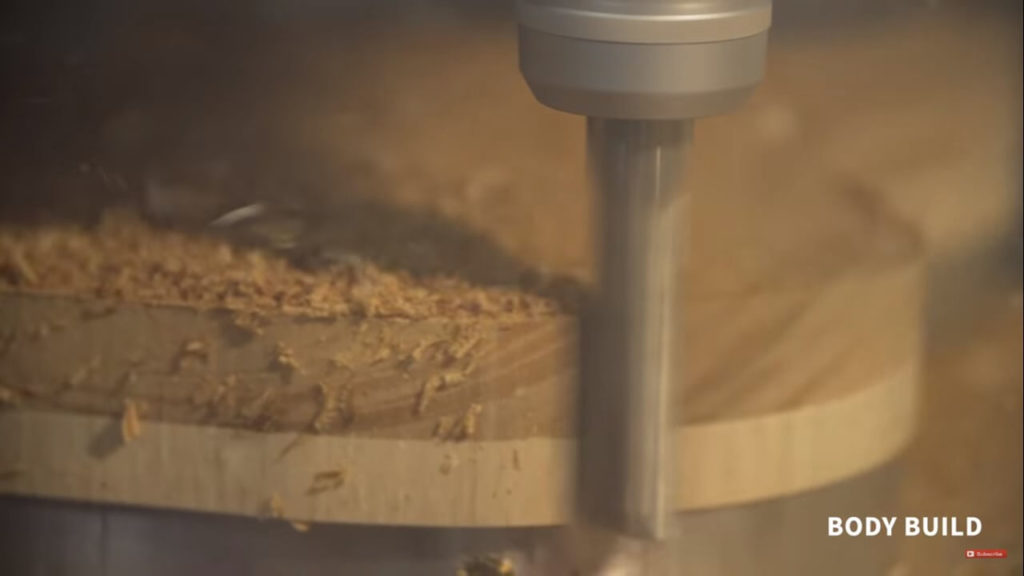
Tallado del cuerpo
Las operaciones de CNC para S2, CE y Core son todas muy similares, excepto por los programas. Utilizamos un tallado de biselado para nuestros cuerpos S2. Usamos un tallado de violín poco profundo para nuestro ver Bolt-on. Y usamos un contorneado para la Silver Sky. Obviamente, utilizamos nuestro tallado de violín tradicional para nuestras guitarras Core.
Los primeros cortes en el CNC son lo que llamamos recortes. El cuerpo se coloca al revés ubicados en los agujeros de trabajo -agujeros que se utilizan para que el cuerpo esté en el lugar que corresponde- que acabamos de perforar, se forma el perímetro exterior del cuerpo, se talla el rebaje de la panza o barriga -belly cut-. Se rutea la cavidad para la electrónica y controles, si hay una cavidad de trémolo el ruteo se hace aquí, los huecos para las tapas traseras y luego el radio para la vuelta en el borde posterior.
La segunda máquina CNC hace todos nuestros cortes superiores, se encargará del tallado del carved de violín, el neckpocket para el mango, agujeros de las pastilas o pickups, agujeros de trémolo, los agujeros para los controles o los agujeros para el puente Stop-tail. Todo esto se hace en esta segunda máquina.
Proceso de lijado
Cuando el cuerpo sale de la máquina CNC, el primer paso es lijar las superficies planas para lo cual utilizamos una lijadora de panel semiautomatizada que ayuda a mantener una superficie plana tanto en la parte superior como en la parte posterior de la guitarra. Después de la lijadora, básicamente estamos lijando un cuerpo que está fuera de una máquina de tallado CNC que tiene marcas de fresado en una superficie terminada que está lista para teñir.
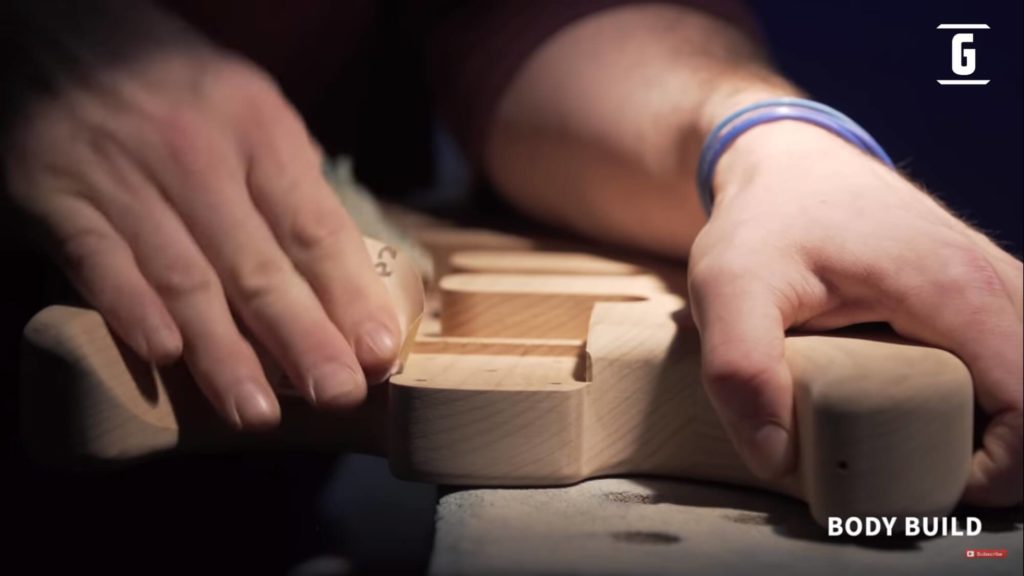
Hay un par de cosas que estamos logrando cuando estamos lijando el cuerpo de una guitarra. En primer lugar, tiene que tener la forma correcta, en segundo lugar, debe estar absolutamente libre de marcas, rayas y rasguños porque ese es nuestro desafío para nosotros mismos: poder mirar una guitarra teñida y decir que no hay defectos, ni rasguños ni nada que reste valor a la belleza del arce tenido que hay en la guitarra.
Encolado de mango
Una de las claves para tener una guitarra muy buena es tener un acabado muy delgado y muy duro y el requisito de que sea posible es que la madera sea absolutamente plana y verdadera.
Encolado de mango
El ensamblaje del cuerpo y mango -llamado «NBA» por sus siglas en inglés- es donde nos aseguramos de que tenga un encastre preciso y ceñido entre el mástil y el cuerpo, se pega el mango con el ángulo exacto para que tengamos la altura adecuada en el trémolo o el puente Stop-tail y nos aseguramos de que el mástil y la posición del puente se alinean con precisión con nuestros medidores de cuerda.
Una vez que se sujetan el mango y el cuerpo, el pegamento se escurre de la articulación del mástil y pasamos mucho tiempo asegurándonos de limpiar no solo lo que está en la superficie, sino que también debemos tener mucho cuidado para obtener cualquier pegamento que se haya depositado en los poros de la madera porque esto va a aparecer dentro de la operación de teñido y pintura y dentro de las operaciones de acabado.
Una vez que el cuerpo y el cuello están pegados, básicamente tenemos una guitarra terminada y básicamente hemos terminado con el trabajo de madera.
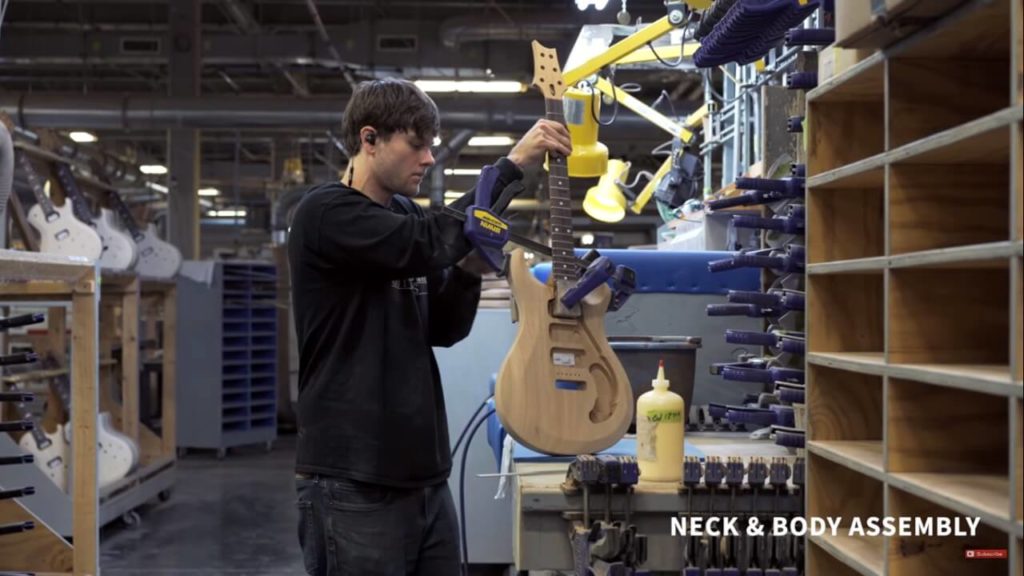
Acabado de la guitarra
Acabados utilizados por PRS
En 1985, cuando comenzamos el negocio, el mercado de la guitarra eléctrica era en gran medida de colores sólidos, muchos neones brillantes realmente llamativos y entramos y dijimos que nuestra firma será colores clásicos de arce rizado -curly maple-, pero colores vibrantes. Guitarras en la cual la belleza de la madera es parte de lo que te atrae hacia el instrumento.
Primeros colores de PRS
Comenzamos la empresa con tres colores. Había un Vintage Yellow -amarillo vintage-, un Scarlet Red -rojo escarlata- y un Royal Blue -azul real. Pero con el tiempo hemos evolucionado esos colores y esos procesos para que sean literalmente cientos y cientos y cientos de colores. Mucha creatividad se ha invertido en la visión de esos colores y en la ejecución de esos colores. En cierto modo, culmina con lo que comenzamos a hacer con nuestros teñidos graduales.
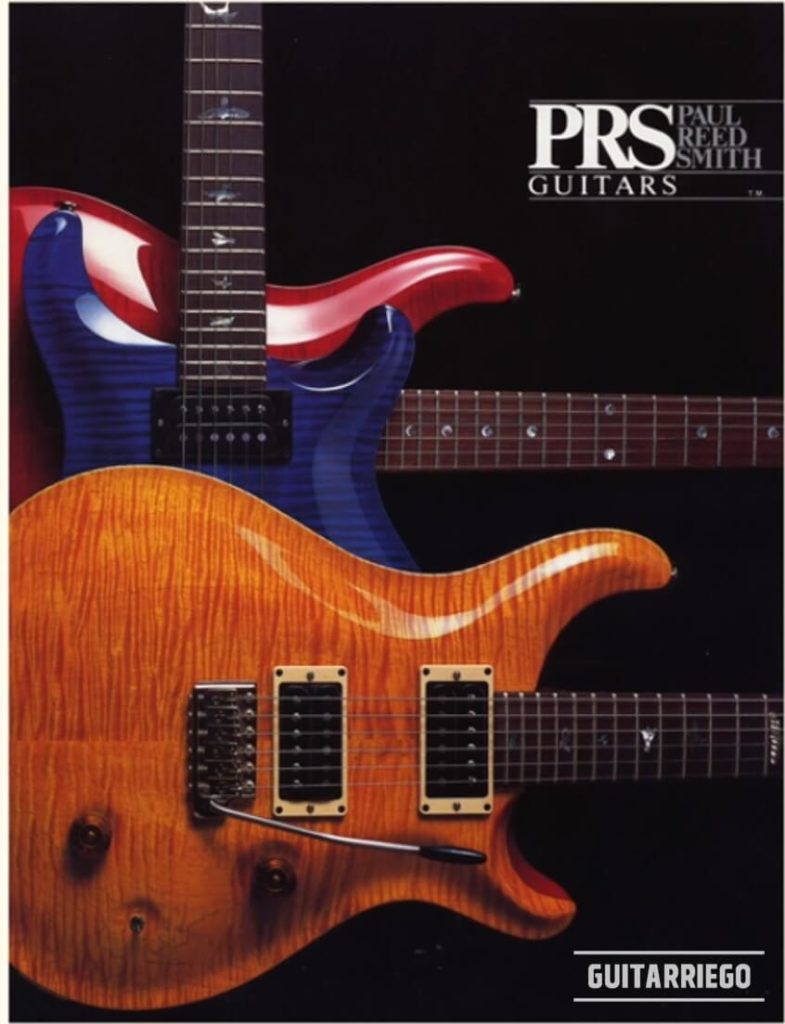
Relleno de poros
Después de nuestro proceso de teñido, vamos al relleno de poros. Usamos una pasta de relleno de poros que se frota en la madera y luego se limpia, lo que rellena los poros abiertos de la madera, para que tenga una superficie plana sobre la cual poner la capa de base. Después del relleno de grano, preparamos la guitarra, la cinta del diapasón y la guitarra está lista para las operaciones de capa base.
Funciones del acabado y su función tonal
Lo que la mayoría de la gente piensa con acabado es una superficie protectora. Estamos de acuerdo con eso, estamos tratando de proteger la guitarra, pero más que nada pensamos que es un proceso tonal. El acabado tiene mucho que ver con cómo sonará la guitarra.
Puedes matar una guitarra cubriéndola con algo que sea muy grueso y no muy duro y cubriéndola por fuera. Y eso es algo con lo que tenemos mucho cuidado dentro de nuestra empresa.
Para asegurarnos que tengamos acabados muy finos, acabados muy duros y asegurarnos que la belleza de la guitarra venga de acabados perfectos. Desde todo punto de vista, una guitarra debe verse bien, sentirse bien y sonar bien y el acabado es sorprendentemente el acabado es una parte importante del cumplimiento estos tres fundamentos.
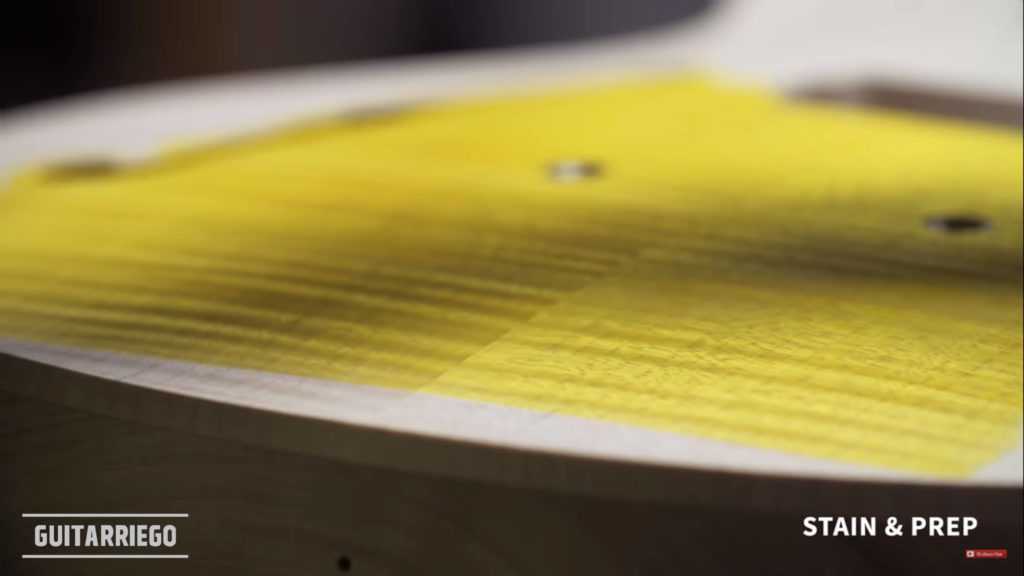
Aplicación de la capa de base
Cuando aplicamos nuestra capa base, esta tiene un cabello humano y medio de grosor. Tiene aproximadamente seis milésimas de pulgada -0,15 milímetros-, no hay mucho material para nivelar, por lo que tiene que ser una capa perfecta. Y la capa base es uno de los lugares donde creemos que una máquina es capaz de hacer el trabajo de manera más consistente y precisa que un ser humano. Debido a que el objetivo de la capa base es simplemente colocar una cantidad muy delgada, muy concisa de material en el instrumento, al igual que una máquina CNC, un robot es capaz de hacer esto día tras día exactamente igual.
Secado y curado de la capa de base
Después de rociar la capa de base, la guitarra se seca y se cura. Después de un par de días lijamos el cuerpo de la guitarra, nivelamos la superficie y se prepara para rociar. Si una guitarra tiene un fondo negro o un tono de fondo o un Sunburst, iniciamos nuestras operaciones de codificación de colores.
Pintado de la guitarra
Un Sunburst perfecto es una forma de arte y se necesita un artista para aplicarlo en nuestras guitarras. Todo el mundo lo hace un poco diferente, puedes mirar nuestras guitarras a lo largo de los años y podemos decir quién fue el rociador que puso un Sunburst particular porque es casi como una huella digital.
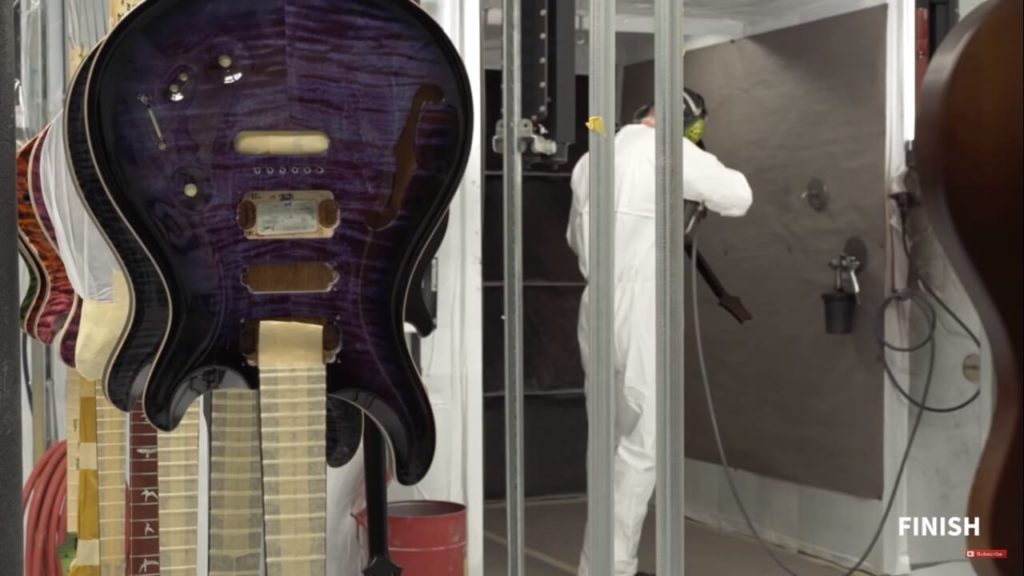
Al final del proceso de pintado del color, si vemos un punto que haya quedado un poco claro o necesita un retoque, podemos ir a nuestra cabina de retoque y aplicar hábilmente un acabado parejo, igualando esa parte posterior o ese mango.
Después del pintado de colores, estamos listos para la capa superior. Con mucho cuidado, un rociador rocía manualmente la capa superior sobre la guitarra. Se necesita un artesano altamente calificado para aplicar el acabado de la manera que necesitamos rociarlo para lograr el aspecto, la sensación y el sonido del instrumento que deseamos.
Cuando terminamos con nuestras operaciones de pulverización, el grosor total de laca en nuestras guitarras es de menos de dos pelos o cabellos humanos.
Nivelado y lijado de trastes
Tomamos el material -lacas- y lo colocamos sobre el mueble, lo lijamos, lo bloqueamos -tapamos los poros de la guitarra-, lo nivelamos la capa de base y luego lo hicimos con la capa superior y al final del proceso, quiero tomar ese diapasón y esencialmente hacer que se sienta cómodo y familiar, y como una guitarra que has tocado toda tu vida y acaba de salir de un estuche.
Hacemos eso a nivel de traste. Aquí también es donde nivelamos los trastes en nuestras guitarras Core usando bastones rectos y nos aseguramos de que los trastes estén absolutamente nivelados entre sí. Después de nivelar los trastes, la capa superior se lijará a máquina, y luego se lijará manualmente la guitarra.
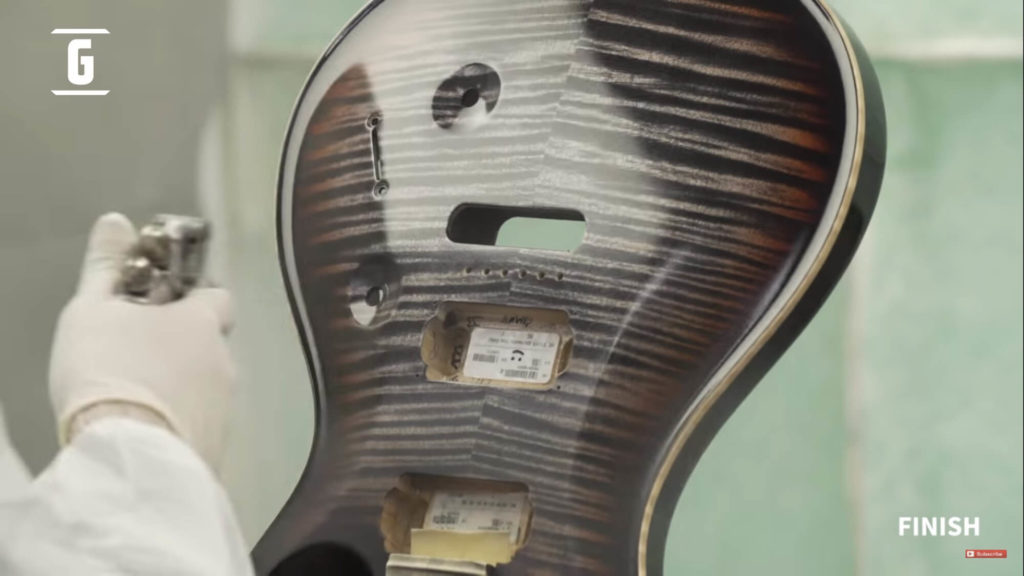
Inspección de la guitarra
Se inspeccionará cuidadosamente y luego entrará en nuestra sala de pulido. Cuando la guitarra sale de la sala de pulido, se revisa cuidadosamente para asegurarse de que no haya fallas, ni problemas en la guitarra. Si vemos algo en este punto del proceso, la guitarra puede retroceder un paso y corregirse o puede abordarse allí en el banco, a esto lo llamamos a este «Turn around» -dada vuelta-.
Lo llamamos Turn Around porque al comienzo del negocio solo teníamos un estante para las guitarras que salían de la sala de pulido. Si la guitarra no estaba lista para el ensamblaje final, se daba vuelta para que mire hacia la sala de pulido. Cuando la guitarra estaba lista para el ensamblaje final, se le daba vuelta y se enfrentaba a la sala de ensamblaje final, así que empezamos a llamarlo dada vuelta y así quedó.
Nuestras guitarras Bolt-on están terminadas de una manera diferente. Obviamente, el mango aún no está en el cuerpo, por lo que el cuerpo y el mango se rocían, pintan por separado. Pasan por la operación de lijado, pasan por la operación de pulido de manera idéntica, pero el mango y el cuerpo se acoplan juntos después del proceso de pulido donde encontramos el par coincidente, verificamos el ángulo del mango y lo atornillamos al cuerpo. Entonces la guitarra está lista para el proceso de Turn Around -inspección-.
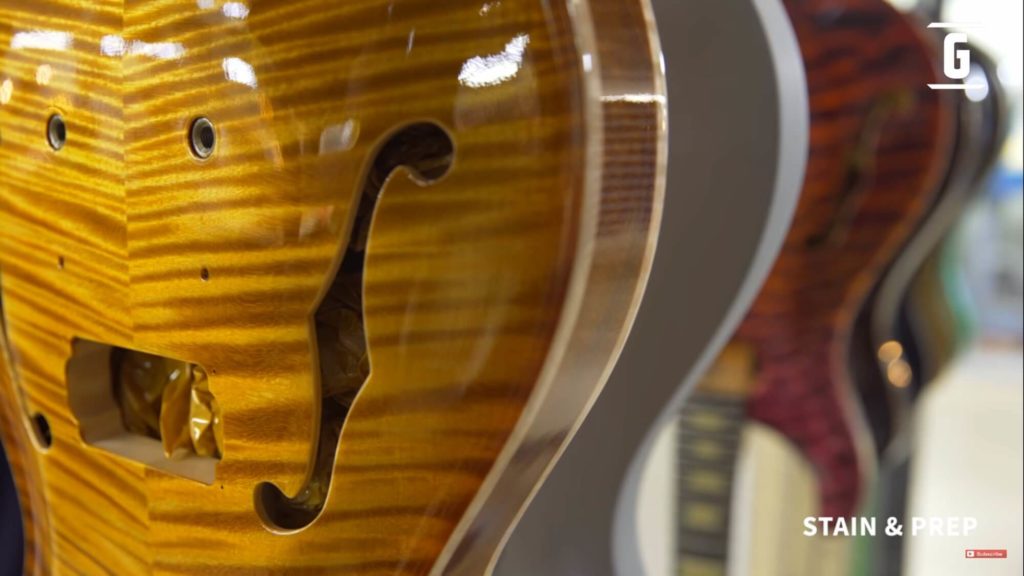
Este es uno de nuestros principales puntos de control para garantizar la calidad. Cuando la guitarra se encuentra con su aprobación, entra en un estante y un armador de guitarras puede seleccionar esa guitarra y comenzar a armarla. Pero antes de que podamos hacer esa guitarra tenemos que ir a la sala de electrónica.
Sala de Electrónica
Cuando entramos en la Sala de Electrónica, lo que realmente estamos haciendo es entrar en una sala llena de soluciones. Cuando Paul Reed Smith comenzó en el mundo de la guitarra, se dedicaba a la reparación de instrumentos. Mientras reparaba esos instrumentos, veía por qué las cosas se rompían o por qué las cosas no funcionaban de la manera que el guitarrista quería, y estaba buscando soluciones a esos problemas.
Finalmente, las soluciones a muchos de esos problemas fueron las que llevaron al diseño de muchas de las partes patentadas que utilizamos. Ya se trate de nuestras clavijas de afinación de bloqueo, nuestro puente de trémolo patentado, el puente de guitarra de Paul con inserciones de latón, las pastillas o pickups que usamos. Cada parte que está en esta guitarra no es única por el hecho de ser única, es única porque sentimos que es la mejor manera de que esa parte o pieza en particular pueda ser diseñada y con los materiales que funcionan mejor para esa guitarra en particular. Están hechos para ser de alto rendimiento en la naturaleza y en la combinación correcta en cada uno de los modelos individuales, se unen para completar la personalidad de ese instrumento.
Sala de ensamblaje
Cuando salimos de la sala de electrónica, entramos en el ensamblaje donde la sala se divide en dos secciones. Una sección para el premontaje y una sección para el ajuste final. El ensamblaje final es donde todos esos componentes se unen con el instrumento y nace la guitarra.
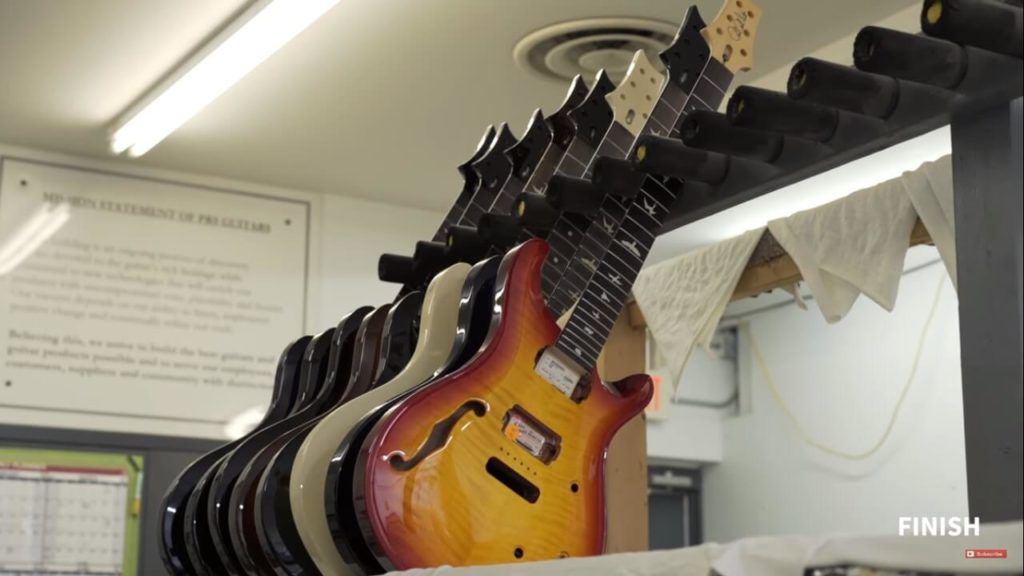
Volviendo a la historia de Paul, creo que lo que nos distingue hasta cierto punto dentro de la industria, es la calidad de nuestros ajustes finales. Además de ser un buen reparador y un gran constructor de guitarras, Paul era muy conocido por sus ajustes y tiene estándares muy exigentes para esas setups. Lo que tiene esta sala es la capacidad de llevar lo Paul hace a un nivel muy artesanal, haciendo que una guitarra se sienta muy especial y perfecta y elevándo eso a un proceso de fabricación.
Después de que la guitarra esté terminada, el ensamblador final completará la etiqueta colgante, firmará su nombre en ella, escribirá los detalles de la guitarra y fechará la guitarra. Luego, la guitarra pasará a nuestra inspección final de garantía de calidad.
Inspección final de la guitarra
No hemos hablado mucho sobre el control de calidad, pero en todos los lugares a los que hemos ido en esta gira ha habido elementos de garantía de calidad y control de calidad.
A lo largo de todo el proceso de fabricación de la guitarra, también verá personas firmando sus iniciales y una guitarra. Lo hemos hecho desde el comienzo de la empresa. En PRS hoy esa tradición continúa, pero hay muchas más firmas porque las guitarras se enfocan en áreas individuales con mucho más cuidado que hace 35 años. Cuando esa guitarra se firma para ir de una etapa a otra, la persona responsable de decir que la guitarra es buena pone sus iniciales en la guitarra.
En la inspección final, la guitarra se prueba tocándola, asegurándose de que todo lo relacionado con esa guitarra esté funcionando de la manera que queremos que lo haga.
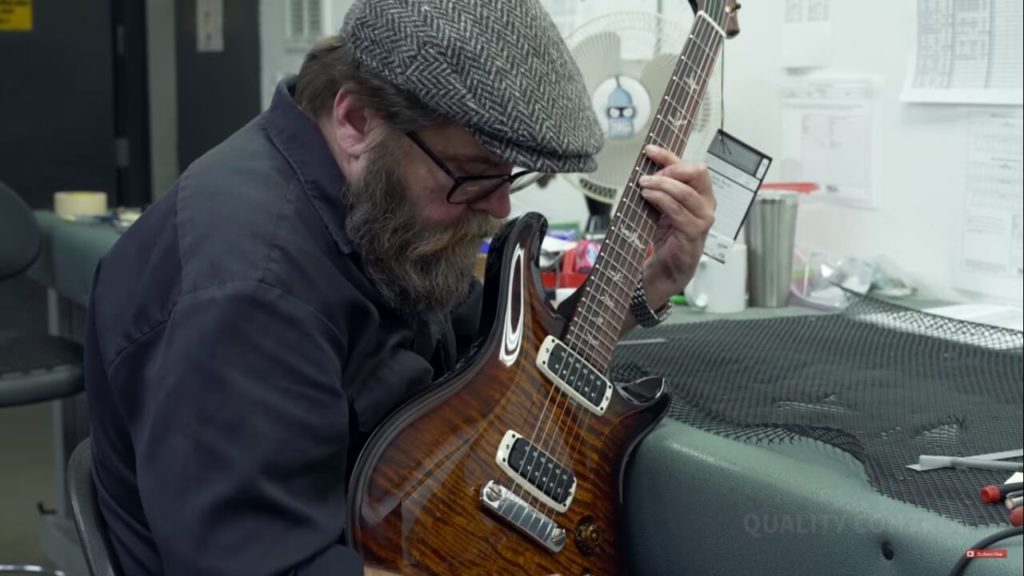
Proceso de empacado
En el empacado final, nos aseguramos de que la guitarra se vea perfecta y que tenga todos los accesorios apropiados con la guitarra. Luego se cierra el estuche, la guitarra entra en una caja, entra en nuestro almacén y se prepara para salir a un cliente.
Inspección al azar de los responsables de fabricación y calidad
Pero hay una parada más en el camino. Los viernes por la mañana vamos a nuestro almacén y seleccionamos al azar guitarras que se están preparando para ser despachadas. Las sacamos de los envíos, las llevamos a nuestra sala de reuniones donde nuestros gerentes de fabricación y garantía de calidad se reúnen y revisan las guitarras para ver dónde estamos parados a nivel de calidad dentro de la empresa. En general, no encontramos problemas con las guitarras, pero lo que tenemos es una oportunidad para pensar en cómo podemos mejorar los procesos o mejorar las guitarras y, a veces, incluso se nos ocurrirán ideas para nuevas guitarras para el futuro dentro de esta reunión.
Despedida y agradecimiento final
Espero que algunos de ustedes decidan venir a PRS y realmente experimentar esto de primera mano. Gracias por mirar el video. Gracias por hacer nuestro recorrido por la fábrica y, sobre todo, gracias por ser parte de la familia PRS. Esperamos verte pronto.
Si te gustó esta nota de la visita a la fábrica de PRS, puedes compartirla en tu red social favorita. También puedes compartir opiniones o charlar sobre esta reseña y más con otros músicos en nuestro foro.
Suscríbete a nuestro Instagram y Facebook para mantenerte al tanto de las novedades.